Der Kolben als eines der wesentlichen Bauteile des Verbrennungsmotors dient der beweglichen Abdichtung des Verbrennungsraums und der Übertragung der Gaskräfte auf den Kurbeltrieb. Hierbei muß gleichzeitig die von den heißen Verbrennungsgasen übertragene Wärme vom Kolbenboden abgeleitet und die durch den Kurbeltrieb entstehende Normalkraft an der Zylinderwand abgestützt werden. Bei Zweitaktmotoren übernimmt der Kolben weiterhin noch die Steuerung des Ladungswechsels.
Die hohe Belastung von Modellmotorenkolben wird an nachstehenden Kennzahlen deutlich:
Modellmotoren | PKW-Motoren | F1-Motoren | |
Kolbengeschwindigkeit: [m/s] | 18 – 25 | 8 – 15 | 25 |
Kolbenflächenleistung: [kW/cm2] |
0,3 – 0,9 | 0,2 – 0,5 | 0,9 |
Literleistung: [kW/dm3] | 150-600 | 50-150 | 220 |
Kolbenwerkstoff
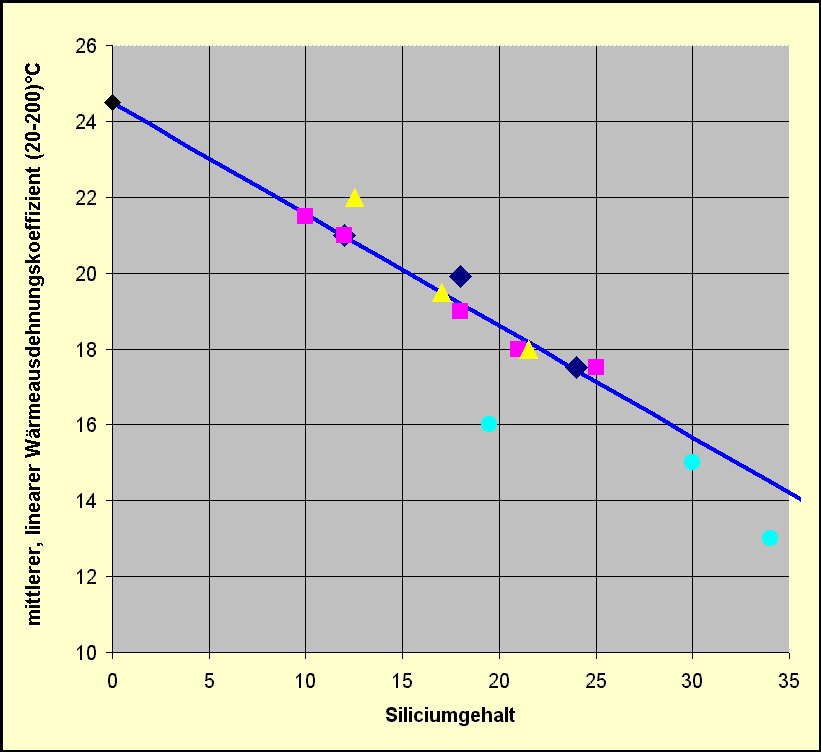
Für hartverchromte Messing-, Bronze- und Aluminium-Zylinderlaufbuchsen haben sich Si-Gehalte von 24 – 30 % bewährt. Kolbenlegierungen mit übereutektischem Gefüge (Si-Gehalt >12,5%) enthalten primär ausgeschiedene Siliciumkristalle deren hohe Härte dem Kolbenwerkstoff ausgezeichnete Verschleißfestigkeit und Fresssicherheit verleihen. Durch pulvermetallurgische Herstellungsprozesse, insbesondere das sogenannte Sprühkompaktieren kann eine Verteilung und Größe der Si-Primärkristalle erreicht werden die optimale Reibparameter und maximale Festigkeiten gewährleisten.
Eine Legierung, die den oben genannten Anforderungen in idealer Weise gerecht wird und in großem Maßstab in modernen Modellmotoren eingesetzt wird ist die von der Fa. PEAK durch sprühkompaktieren hergestellte Aluminiumlegierung DISPAL S 226. Mit Modellmotoren deren Kolben aus dieser Legierung bestehen sind zahlreiche Weltrekorde aufgestellt und mehrere Weltmeistertitel errungen worden. Sie kann (auch in kleineren Mengen) von der Fa. Liquidyn (www.liquidyn.com) bezogen werden.
Kolbendesign
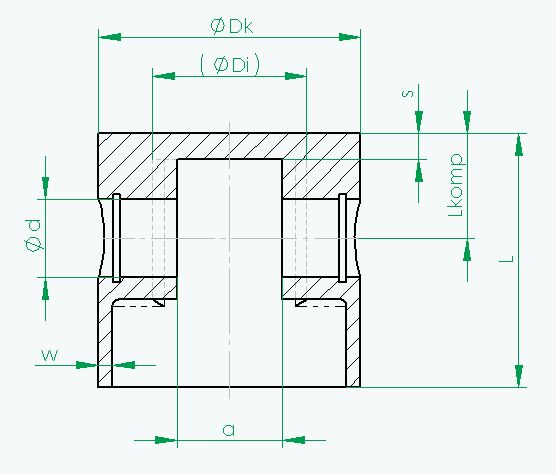
– gesamte Kolbenlänge: L ~ s + (0,5 ….. 1)mm
– Kompressionshöhe: Lkomp ~ (0,4 ….. 0,45) * Dk
– Augenabstand: a ~ (0,4 ….. 0,45) * Dk
– Durchmesser der Kolbenbolzenbohrung: d ~ (0,28 ….. 0,35) * Dk
– Wandstärke des Kolbenschafts: w ~ (0,04 ….. 0,1) * Dk
– Wandstärke des Kolbenbodens: s ~ 0,07 * (Di * pz)½ (für DISPAL S 226 T6)
Di: Innendurchmesser des Kolbenbodens (mm)
pz: maximaler Zünddruck (MPa)
Kolbenbearbeitungstipps
* Vor der Fertigbearbeitung des Kolbenaußendurchmessers (einpassen) sollten die bearbeiteten Kolben einer mehrstufigen Wärmebehandlung unterzogen werden, um eingebrachte Bearbeitungsspannungen zu verringern und die Volumenstabilität (“Wachsen”) des Materials im Motorbetrieb zu erhöhen. Das “Wachsen” des unbehandelten Materials im Motorbetrieb entspricht der thermischen Ausdehnung bei (10-20)°C Temperaturerhöhung. Eine in 4 Sufen von 120°C bis 180°C gesteigerte Wärmebehandlung mit Ofenaufheizung und -Abkühlung des Kolbenmaterials sowie einer Haltezeit von etwa 3 Stunden hat sich hierbei bewährt.
* Die Abweichung der Kolbenbolzenbohrung von der Senkrechten zur fertigbearbeiteten Zylindermantelfläche des Kolbens sollte 0,005mm nicht überschreiten.
* Eine Abweichung der Spaltgeometrie zwischen Zylinder und Kolben von (0,001 bis 0,002)mm bedeutet einen Leistungsverlust von ca. 5% (bei Motoren ohne Resonanzrohr).